Energy saving and environmental protection have become an inevitable trend in the development of the automobile industry in the 21st century. Automobile lightweight is an effective way to realize energy saving and environmental protection. Composite materials have played an important role in the process of automobile lightweight. The report of the World Aluminum Association pointed out that for every 10% reduction in the quality of the car itself, the fuel consumption can be reduced by 8%. The traditional ordinary steel body structure can reduce weight by more than 10% through structural optimization design and the use of high-strength steel plates. The use of all-aluminum body can achieve a weight reduction effect of more than 25%, and the use of fiber-reinforced plastic composite materials can achieve a weight reduction of more than 50%. Heavy effect. Most of the existing car tailgates are formed by sheet metal stamping and welding, with a large number of parts, high quality, and low degree of freedom in modeling. Plastic composite materials are widely used in automobile lightweight due to their low density, specific rigidity and high specific strength. In recent years, many lightweight plastic tailgates have appeared. Compared with traditional automobile sheet metal tailgates, they have the following advantages:
(1) Lightweight: By using fiber-reinforced materials to replace traditional steel materials, while considering the overall integration and optimization of plastic tailgate parts, the mass can be reduced by 30%-50% (5-8 kg). In addition, the reduced quality of the car can bring a good user experience: reduced fuel consumption/ increased cruising range, improved acceleration performance, reduced operating force for opening and closing the tailgate, etc.
(2) Novel shape: Due to the variable thickness of the fiber reinforced material and the high degree of freedom of shape, the appearance shape that may not be able to be manufactured by using traditional materials can be realized. The complex modeling curve and stylish and beautiful appearance of the plastic tailgate can meet the increasing requirements of users for car styling
(3) Integration: The use of plastic tailgates reduces the number of parts of the tailgate, and the interface and gaps of the tailgate are removed to enhance the sense of integration of the tailgate components; in addition, the use of plastic tailgates can improve manufacturing efficiency: no more stamping workshops Stamping is required; the painting workshop does not need tailgate painting, which reduces the coating process beat; at the same time, after using plastics, the overall injection molding can be achieved with high strength and light weight, which greatly reduces the number of parts and reduces the assembly pressure of the assembly workshop, as listed in Table 1. The composite material tailgate has the advantage of manufacturing process compared with the traditional automobile tailgate integration.
The plastic tailgate has strong corrosion resistance, no electromagnetic interference to automotive electrical components, good flexibility, and can be restored in low-speed collisions. It not only reduces the probability of maintenance, but also saves maintenance costs .
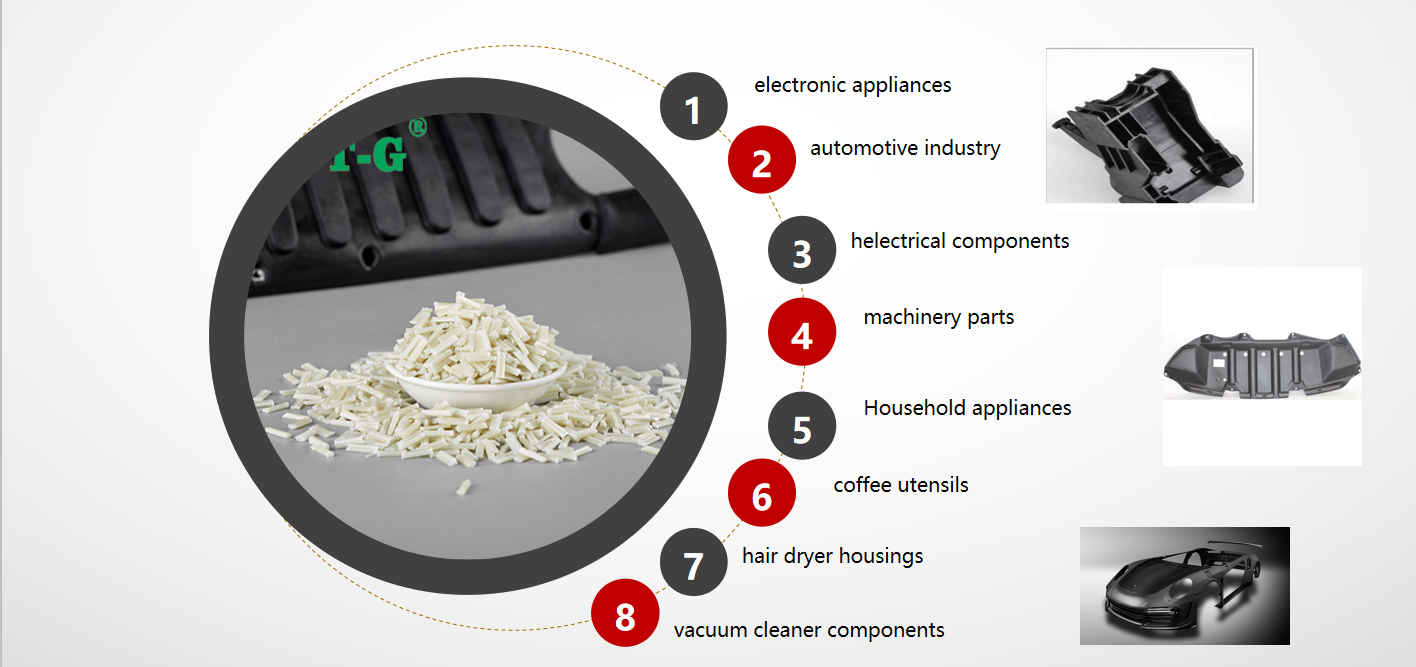
Plastic tailgates mainly have the following shortcomings:
(1) High cost. Although the cost of composite tailgate molds is lower than that of traditional sheet metal tailgates, the cost of using composite materials is 3 to 5 times that of traditional sheet metal parts. As a result, the cost of the tailgate assembly is higher than that of the sheet metal tailgate;
(2) The main engine factory lacks plastic tailgate development experience, and the analysis specifications and evaluation indicators suitable for composite materials need to be improved.
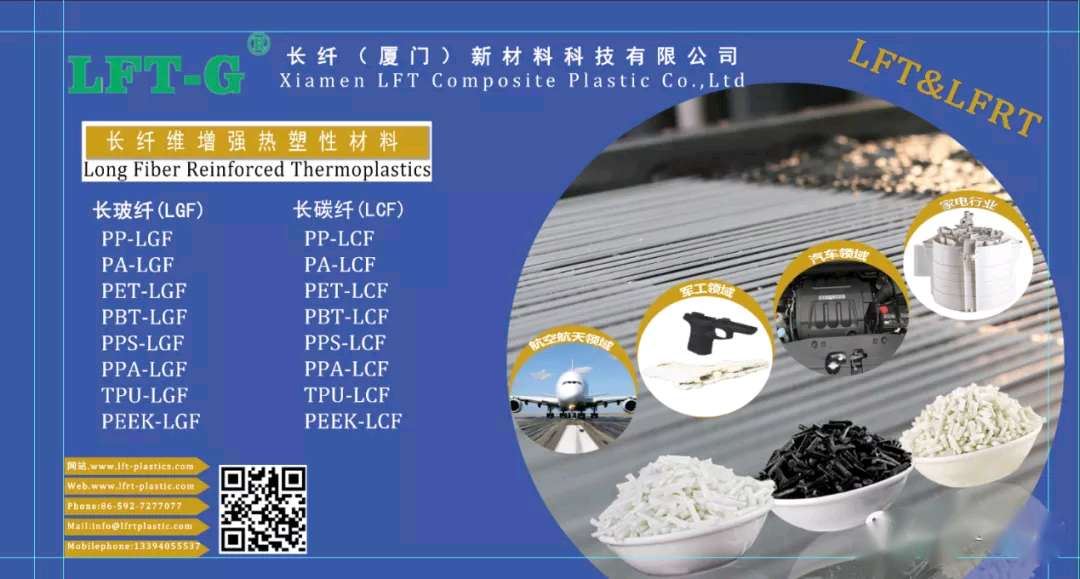